SOLUTIONS
Reliability Centred Maintenance
RCM assessments identify cost effective maintenance strategies based on a detailed understanding of an asset's functional requirements, performance standards and conditions of use. If applied correctly, the resultant maintenance strategy will ensure that the required levels of safety and in-service availability are achieved at minimal cost.
MES, RCM consulting specialists, have the skill base and project experience in the application of RCM methodology. This is centered around:
- Derivation of functional definitions and performance standards
- Analysis of source data to identify trends and failure characteristics
- Failure Modes Effects and Criticality Analysis (FMECA) whereby functional failures are defined and failure modes identified together with the consequential effects relative to safety, environmental and system performance
- Based on FMECA results and the failure characteristics of individual equipment and components, derivation of cost effective maintenance strategies can be achieved using:
- On condition maintenance
- On failure maintenance
- Scheduled overhaul / replacement
- Fault finding
- Re-design where appropriate and cost effective
- Preparation of maintenance documentation including scheduling
Derivations of maintenance strategies by MES consultants, using RCM techniques offer the following benefits:
- Maintenance strategies tailored to suit specific commercial and operational requirements
- Optimisation of maintenance costs
- Efficient use of maintenance resources
- A clear audit trail and demonstration of compliance with safety case or other regulatory / legislative requirements regarding the in-service availability of critical equipment
Our RCM consultants are able to provide:
- Reliability Centered Maintenance (RCM) studies
- Maintenance Optimisation
- Root Cause Analysis
- Failure Modes Effects and Criticality Analysis (FMECA)
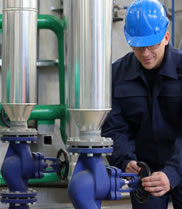
SECTOR STUDIES
- Hazard Identification (HAZID) Workshop
- Hazard and Operability (HAZOP) Workshop
- Preliminary Hazard Analysis (PHA) Workshop
- Offshore Activities Risk Assessment Review
- BOWTIE Workshop
- Failure Modes Effects and Criticality Analysis (FMECA) Workshop
- Reliability Operability Maintenance (ROM) Workshop
- Environmental Identification (ENVID) Workshop
- Best Available Techniques (BAT) Workshop
- Safety Integrity Level (SIL) Workshop
- Layers of Protection Analysis (LOPA) Workshop
- Fire and Explosion Hazards Analysis (FERA/FEA/FRA/FEDHA)
- Gas Dispersion and Smoke Ingress (GDSI) Analysis
- Exhaust Vent Study
- Escape, Evacuation and Rescue Analysis (EERA)
- Emergency Systems Survivability Assessment (ESSA)
- Temporary Refuge Integrity Analysis (TRIA)
- Non-Hydrocarbon Hazards Analysis (NHHA)
- Dropped Object (DOS) and Material Handling Study
- Ship/Helicopter Collision and Structural Failure Study
- Transportation Risk Assessment (TRA)
- Blast and Overpressure Analysis
- Topsides/Riser/Subsea/Ship Safety Analysis
- Fire, Heat and Smoke Detection System Design
- Active Fire Protection (AFP) Design
- Passive Fire Protection (PFP) Design
- Fire and Gas Mapping
- Fire Dynamics Analysis/Fire Effects Modelling
- Quantitative Risk Assessment (QRA) for Onshore and offshore Facilities
- Offshore/Onshore Pipeline QRA
- Miscellaneous Risk Assessments (eg. Temporary Buildings, Transportation, etc.)
- Simultaneous Operations (SIMOPS) Risk Assessment
- Cost-Benefit Analysis (CBA)
- ALARP Assessment
- Offshore HSE/Safety Case Development
- Onshore COMAH/CIMAH Report Development
- HSE/Safety Case Updates/Revisions and Bridging Documents
- HSE MS Audits and Reviews
- Hazard and Risk Register Preparation
- Emergency Response Plan (ERP) Development
- Procedures for General Safety, Operations and Maintenance (SOP) Development
- Performance Standards (PS) Development for Safety Critical Elements (SCES)
- Safety Strategy and Philosophy Development
- Onshore and offshore Facilities Surveys and Audits
- Working Environment Risk Assessment (WERA)
- Human Error and Human Factor Study
- Job/Task Hazard Analysis (JHA)
- Study of Human Behaviour during MAE
- Ergonomics Study
- Environmental Impact Assessment (EIA)
- EIA Scoping
- Availability Studies
- Markov State Modelling
- Logistics and Transportation Using "Real Time" Simulation Modelling
- Debottlenecking and Performance Improvement Studies
- Spare Parts Optimisation Studies
- System Performance Evaluations
- Whole Life Cycle Costing Evaluation
- CAPEX and OPEX Economic Calculations
- Risk Based Inspection Services
- Reliability Centered Maintenance (RCM) Studies
- Maintenance Optimisation Studies
- Root Cause Analysis
- Verification and Validation
- Functional Safety Assessments
- SIS Design
- Safety Requirement Specification Development
- Functional Safety Audits
- Fundamentals of Functional Safety Training
- Safety Integrity Level (SIL) Determination Training
- Layer of Protection Analysis (LOPA) Training
- Introduction to Reliability Concepts, Principles and Applications Training
- Advanced RAM Analysis Training
- Reliability Measurement and Improvement Training